An important ally for hospitals and people in need of medical care
Oxygen is used frequently in general medicine, for medical and emergency assistance. Gas cylinders have been supporting the Healthcare business to help patients with respiratory difficulties, in hospitals as well as for the domiciliary homecare markets and have become more dominant as years go by.
Since 1972 Faber has been designing and manufacturing high-pressure cylinders for people in need of oxygen therapy in hospitals and domiciliary environments i.e. for a period of almost half a century!
The recent COVID-19 pandemic has brought new challenges by causing a spike in demand for medical cylinders that could be barely matched by the supply side; in fact the healthcare industry experienced a shortage of oxygen cylinders all around the world.
Faced with a shortage of cylinders, during this period of emergency in which the demand for oxygen cylinders had increased exponentially, with a huge number of patients having to be treated with oxygen; Faber was a crucial partner of the medical supply chain. Furthermore, despite the COVID-19 lockdown in Italy, production and delivery times have been significantly improved and thanks to the commitment and response from our dedicated employees, Faber was been able to deliver many tens of thousands of cylinders in a very short time. Concurrently, Faber implemented all the stringent measures and provisions sanctioned by the Italian Government’s legislation to protect the health and safety of its staff and reduce the risk of circulation of COVID-19. Faber also activated a comprehensive insurance policy for the benefit of all its employees, which combined a package of hospitalisation and convalescence allowances, in addition to post-hospital care. In the end, fortunately, not one of the 400+ employees has yet contracted COVID. For its compassion towards its employees, Faber was nominated by the Unions for its safety-related best practices. This approach was broadcasted on 1st May (Labour day) on a national TV programme.
Apart from the COVID-19 crisis, the growth in the number of patients with respiratory problems and the continued prevalence of chronic respiratory diseases, due to an ageing population and pollution, is significantly increasing the demand for high-performance cylinders: in terms of lightness, capacity, duration and of course, safety. In this context, Faber, by working closely with its customers, has identified an appropriate response to the market’s requests. The needs of the end users were met by using a unique plate manufacturing route, resulting in ever sophisticated, safe and lightweight cylinders which allow a better performance and experience.
This has been achieved by utilising products with composite materials, at workimg pressures of 300 bar or higher. An extension of this concept is already in place in the industrial gases sector where the working pressure has increased from 200 to 300 bar and is the new industry norm.. This is also true for oxygen and medical gases, where in some countries, such as UK and Australia, such advanced gas packages working at 300 bar, have been in service for more than 25 years with a spotless track record and interesting case studies.
The main benefits of moving from a working pressure of 200 to 300 bar can be
summarised as follows:
- Approx. 50% more oxygen in the cylinder with the same volume
- Reduction of cylinder weight for patient comfort
- Duration of the oxygen therapy will increase by approx. 50% with better patient comfort and experience
- Fewer number of cylinders need to be stocked compared with the usual ones
- Fewer cylinders to be transported and filled meaning less CO2 produced during operations.
Established in 1969 and operating since 1972, Faber has grown rapidly to become the world's leader in the production of cylinders (Types 1, 2, 3 & 4) and systems for the storage of High-Pressure Gases for the Clean Energy (CNG and H2), Industrial and Air Breathing sectors. The world over, with a production capacity of a million cylinders, Faber has earned the best reputation for its high standards of quality and for its capability to comply with the most stringent specifications set down by International Bodies, Local Authorities and its customers.
Cividale del Friuli, 20/07/2020
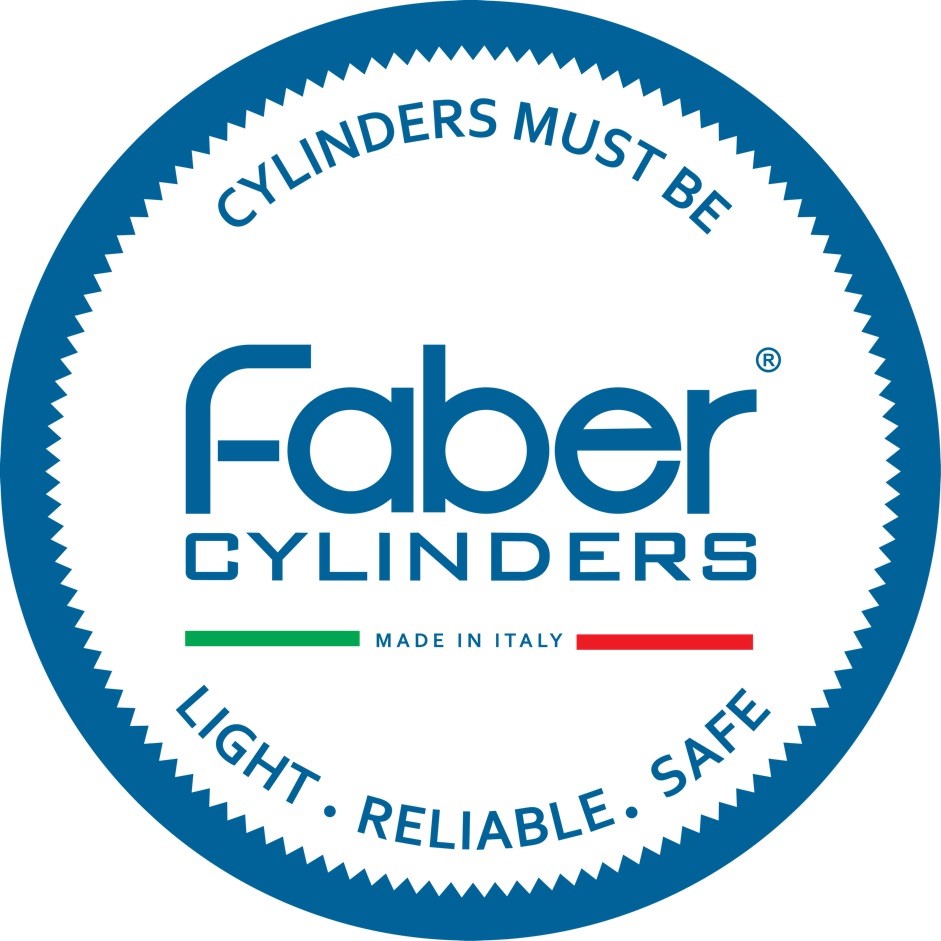
share this article