we perform in-house
all the required tests
for prototypes
and production batches
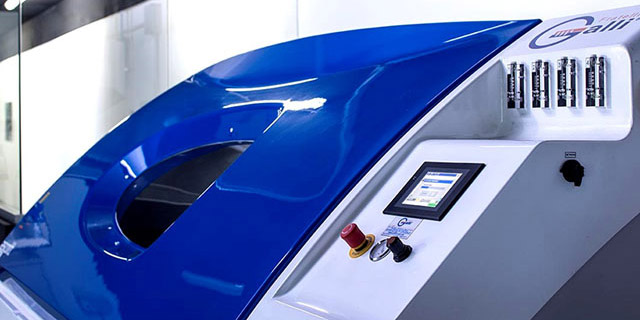
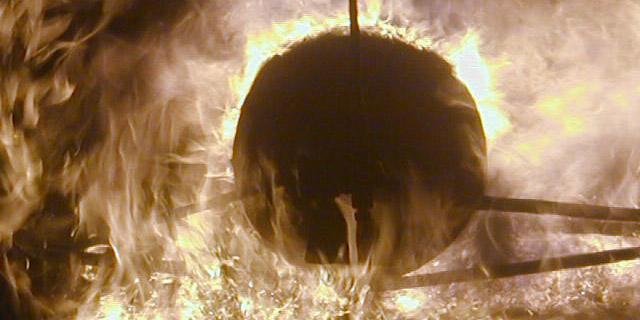
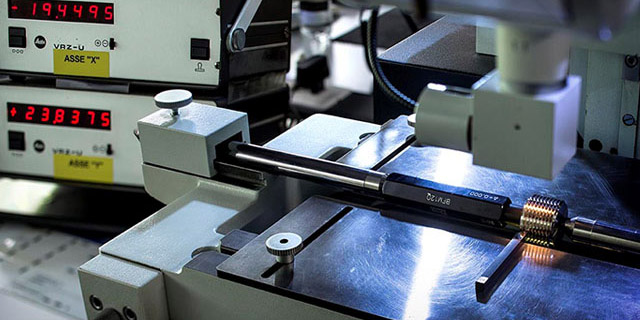
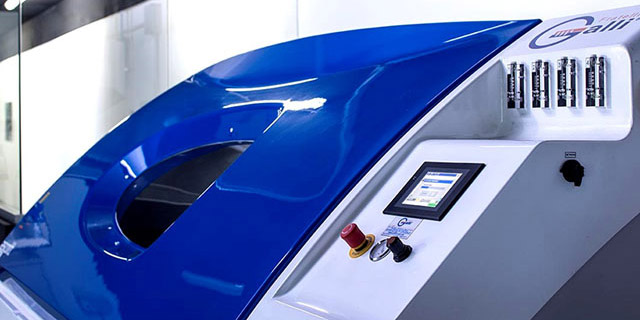
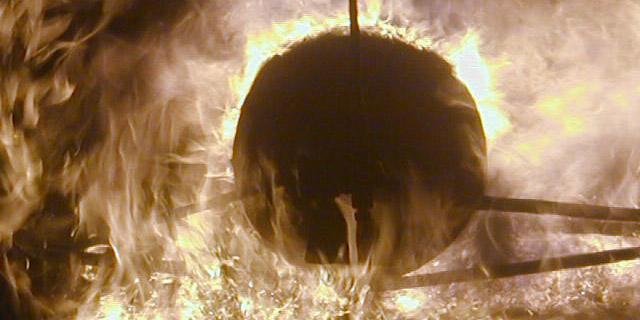
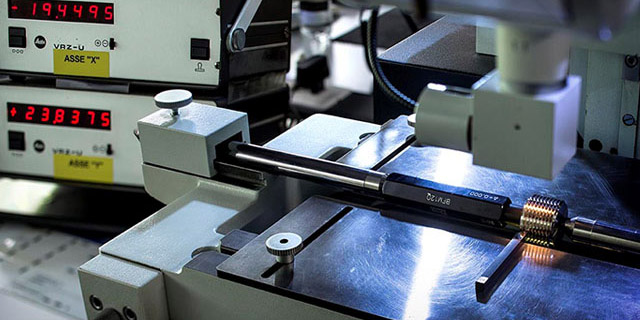
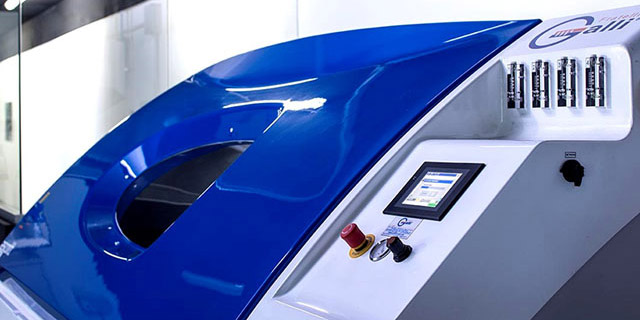
Faber’s test laboratory is probably the best of its kind with a gas cylinder manufacturer anywhere in the world.
We make this claim as, apart from the usual range of test machines and microscopes needed to fulfill the requirements of the range of standards that we manufacture gas cylinder to e.g. EN ISO 11439; EN ISO 9809 series; ISO 11119 series, to name but a few, we also house a unique facility.
The latter establishes the safety of extremely high pressure cylinders (up to 1100 bar working pressure) for use
with gaseous hydrogen. Here Faber’s competent engineers have constructed a cell in which, under a
high purity hydrogen atmosphere, we can test samples for a variety of test methods such as Slow
Strain Rate Test, fatigue crack growth rate, fracture toughness etc. at pressures up to 1100 bar. Here
we can perform tests at temperatures as low as -20°. Both metallic (for steel cylinders) and non-metallic
(for composite cylinders) materials can be tested in this unique cell. The chamber in which the
hydrogen cell is housed, has been constructed such that the above test programs are undertaken with
utmost safety in mind. Such that a sacrificial wall in the chamber will give way, in case of any sudden
release of pressure. The materials selected for the cell’s components have been carefully selected so
that they have all got resistance to the hydrogen embrittlement phenomenon.
Also within our facility we can pressure cycle to failure (up to 2000 bar) and burst test (up to 4000 bar) actual size cylinders. The Hydrogen cycling test can be performed setting the temperature of the gas at -40°C and the pressure of 875 bar. Our Cividale based test laboratory is capable of performing advanced tests on cylinders such as environmental testing, extreme temperature tests, flawed burst tests, bonfire/high velocity impact tests (gunfire), gaseous pressure cycling test etc. Additionally a number of material tests such as Sulphide Stress Cracking (SSC), assessment of corrosion of coatings, characteristics of permeation of plastics etc are continuously performed.
Our suite includes a world beating equipment extremely valuable to car companies who require critical
dimentional data.
This instrument, a “Coordinate Measuring Machine (CMM)” has brought much
success to a number of leading OEM’s around the world.
To date a number of large Industrial gas companies and motor vehicle manufacturers have made use of this unique facility based at Faber.
TEST ON MATERIALS
1. Tests on metals
mechanical tests - strength (yield and tensile), elongation, Charpy impact, toughness, sulfide stress-cracking, chemical analysis, hardness
2. Tests on composite material
tensile (strength and modulus), interlaminar shear strength, resin gel time, specific gravity, viscosity, weight of resin and fiber, barcol hardness
3. Coating performance tests
salt spray, cycling corrosion, cathodic disbondment, adhesion
4. Microscopic examination
TEST ON CYLINDERS
Hydrostatic pressure burst test, Flawed burst test, Flawed cycling test, Ambient temperature pressure cycling test, Hydrostatic pressure burst test, Bonfire test, Penetration test, Flaw tolerance test, High temperature creep test, Accelerated stress rupture test. Permeation test, Natural gas cycling test, Impact damage test (drop test) Leak test, Leak before break (LBB) test, Metrological measurements
HYDROGEN LABORATORIES
We have a unique equipment set in our facilities to perform all required tests for Hydrogen
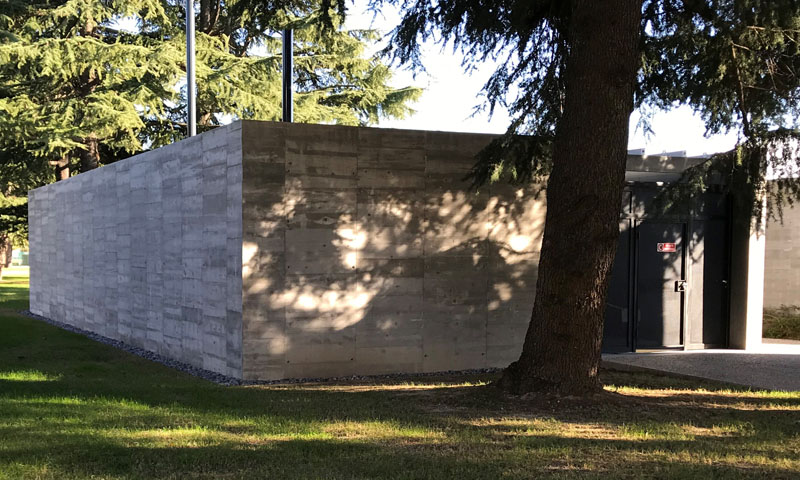
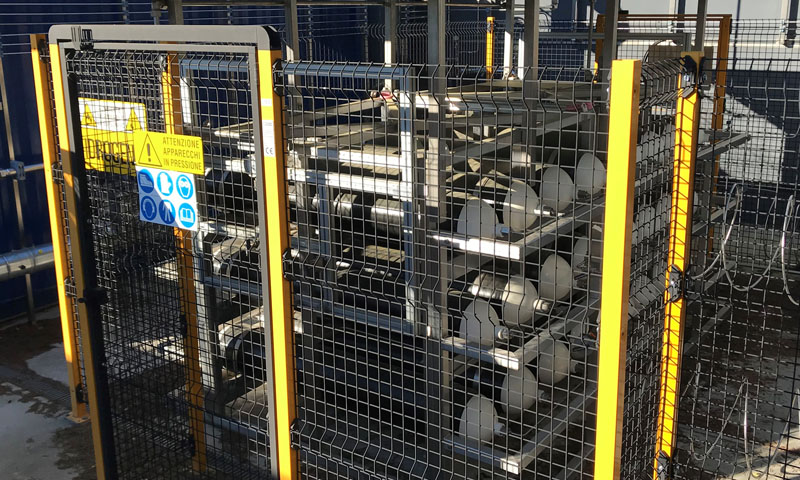
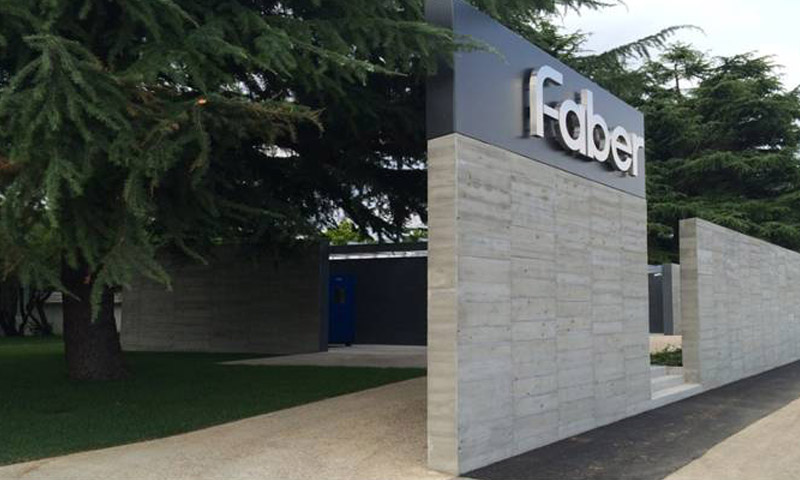
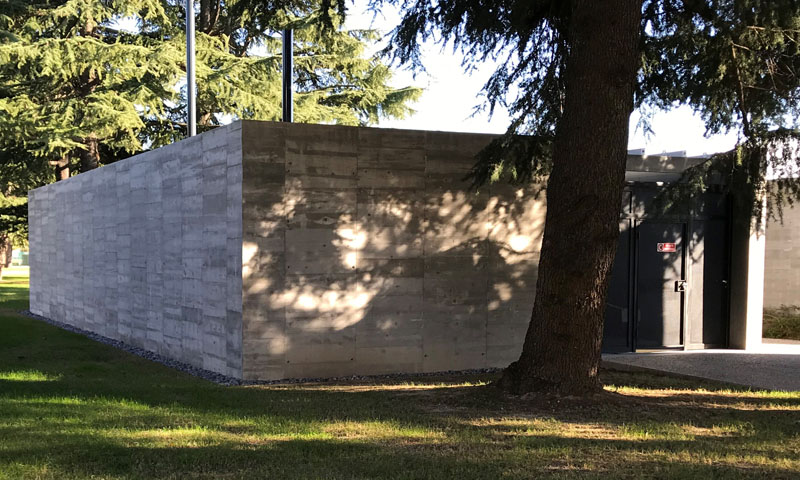
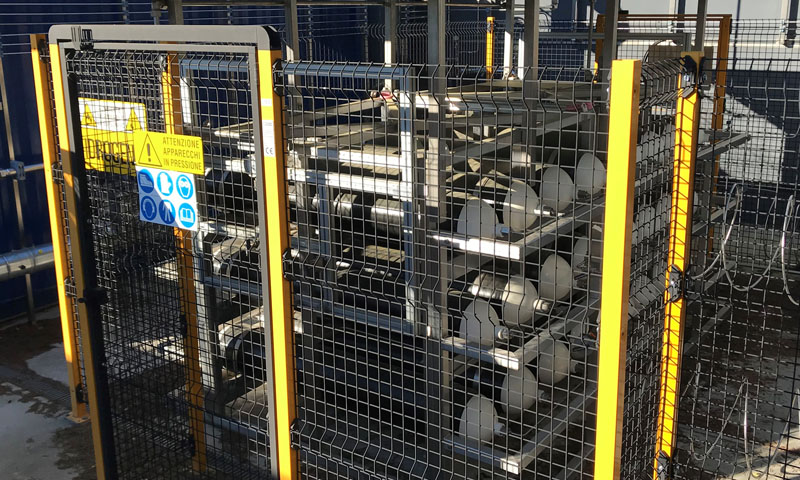
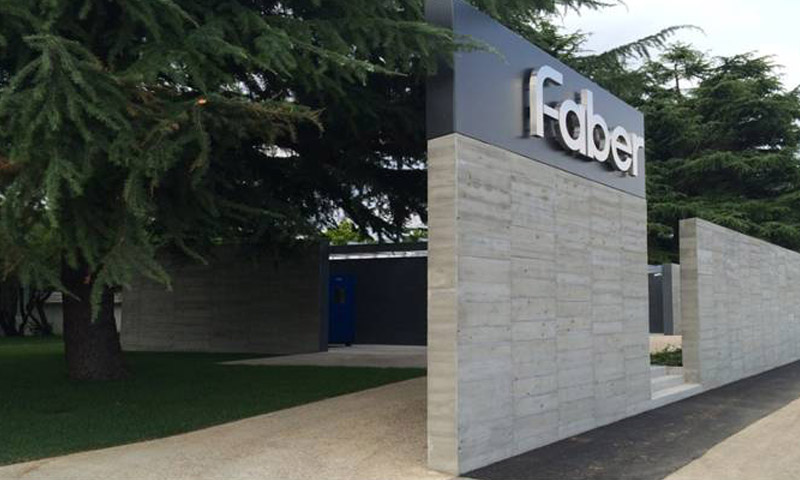
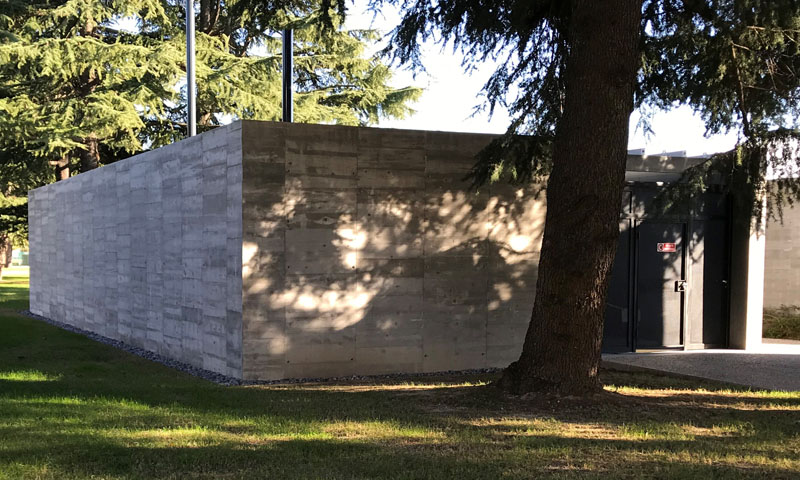