Faber: Our Laboratory’s Capabilities
Based near Venice in Cividale, Italy, Faber produces all four “Types” of cylinders i.e. seamless, Type1; Types 2 and 3: metal lined hoop and fully-wound composite cylinders respectively; as well Type 4 which are non-load sharing plastic lined composite cylinders. We also utilize starting materials ranging from the highly efficient plate route, to that of billet extrusion and even at time, hot spinning from a tube stock.
We are also proud to have a set of very discerning customers ranging from major Industrial Gas Companies, through to worldwide Vehicle Manufacturers and members of the General Public for our diving cylinders. The latter, coupled with a huge product range, implies we should be capable of performing the vast range of testing which is a mandatory requirement of many of the standards (see below) we work with. This we do for almost a million cylinders/annum in our laboratories.
Our Laboratories
Faber’s does not possess just a single test laboratory but a suite of unique test laboratories; they are best appreciated when one views them.
We believe they are the “Best in Class” within the global gas cylinder manufacturers community.
Our claim is based on the fact that apart from the extensive range of test machines and microscopes needed to fulfill the requirements stated in the standards that we utilize (see below) we also house a unique facility.
The latter establishes the safety of extremely high-pressure gaseous hydrogen cylinders.
Here Faber’s competent engineers have developed a cell in which, under high purity hydrogen, we can test samples for a variety of test methods. Examples include; slow strain rate test (SSRT), fatigue crack growth rate, fracture toughness etc. at pressures up to 1000 bar and at temperatures as low as -20°. Both metallic (for steel cylinders) and non-metallic (for composite cylinders) materials are being tested in this unique cell. The hydrogen cell’s overall chamber has been constructed with utmost safety in mind. When undertaking the above test programs: a sacrificial wall in the chamber will yield, away from the main site, in case of a sudden pressure release. The materials selected for the cell’s components have been meticulously selected, all having resistance to the hydrogen embrittlement phenomenon.
Also, within our laboratory we can fatigue full-size hydrogen bearing cylinders to failure up to 2000 bar and burst test them up to 4000 bar. Our Cividale based test laboratories are capable of advanced testing cylinders for varying environmental conditions, extreme temperatures, flawed burst simulation, bonfire/high velocity impact (gunfire) tests, gaseous pressure cycling tests etc. Additionally, a number of material tests such as full chemical analysis, Sulphide Stress Cracking (SSC), assessment of corrosion of coatings, characteristics of permeation of plastics etc. are continuously performed.
Our suite includes a world beating equipment, extremely valuable to car companies, who require critical dimensional data. This unique facility based at Faber, a “Coordinate Measuring Machine” (CMM) has been used by a number of leading OEM’s around the world and Industrial Gas Companies, to whom it has brought much success.
The Standards
The suite of standards we use in Faber is vast! This reflects our worldwide customer base and the wide range of industries who are our long-term customers.
For seamless industrial gas cylinders, the workhorse series of EN ISO 9809 and EN 1964 feature prominently, though these are gradually being replaced by the even more efficient composite cylinders, via the ISO 11119 series. Additionally, for on-board vehicle fuel use, the purpose-built EN ISO 11439 is in widespread demand. Some countries need cylinders made to their national standards and these include for USA a suite of DOT specifications such as -3AA, -3HT or ANSI NGV2-2007, ASME Sect. VIII & Sect X.; for S. Korea KGS C024; for Japan KHK S 0121 to name but a few. The latter production based standards, are to be viewed with our accreditations to ISO 9001, ISO 14001, OHSAS 18001 and IATF 16949 (for the critical motor vehicle industry). Naturally we are also approved by leading Global Inspection Bodies to International Regulations such as the PED (C€ mark); TPED (π mark);
Established in 1969 and operating since 1972, Faber has grown rapidly to become the world's leader in the production of cylinders (Types 1, 2, 3 & 4) and systems for the storage of High-Pressure Gases for the Clean Energy (CNG and H2), Industrial and Air Breathing sectors. The world over, with a production capacity of a million cylinders, Faber has earned the best reputation for its high standards of quality and for its capability to comply with the most stringent specifications set down by International Bodies, Local Authorities and its customers.
Cividale del Friuli, 07/03/2019
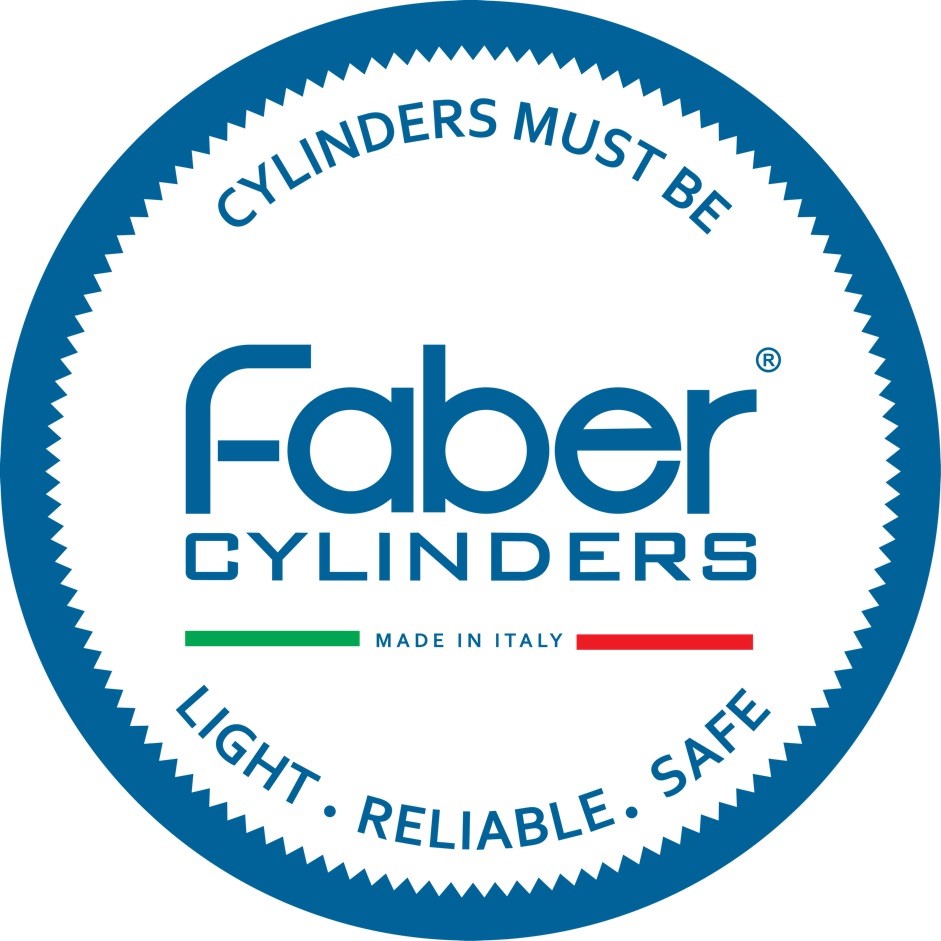
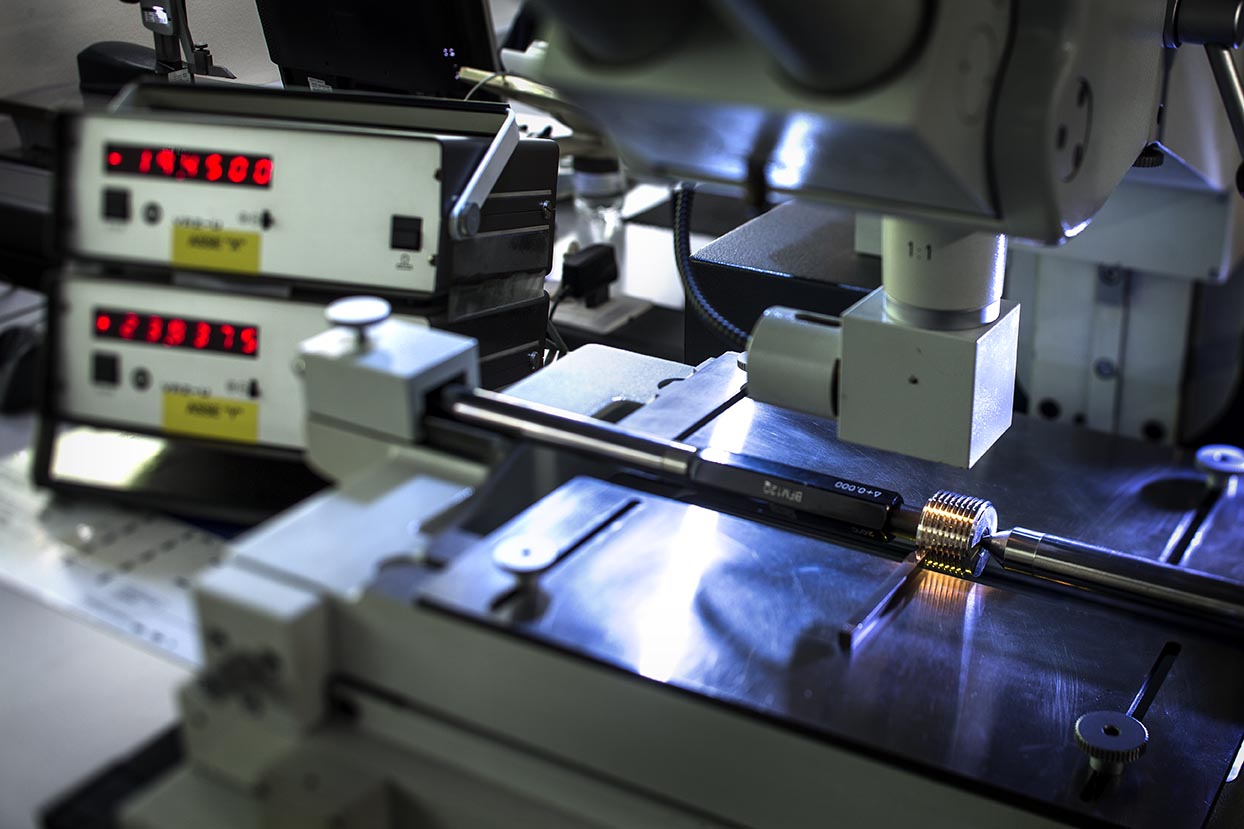
THE SUITE OF UNIQUE TEST LABORATORIES
share this article